Why plastic extrusion is perfect for mass production
Why plastic extrusion is perfect for mass production
Blog Article
Recognizing the Basics and Applications of Plastic Extrusion in Modern Production
In the realm of modern manufacturing, the strategy of plastic extrusion plays a crucial function - plastic extrusion. This intricate procedure, involving the melting and shaping of plastic via specialized passes away, is leveraged across numerous industries for the creation of varied items. From automobile components to durable goods product packaging, the applications are huge, and the possibility for sustainability is similarly excellent. Deciphering the principles of this process discloses real convenience and potential of plastic extrusion.
The Fundamentals of Plastic Extrusion Process
While it may appear complicated, the fundamentals of the plastic extrusion procedure are based upon fairly uncomplicated concepts. It is a manufacturing process where plastic is thawed and afterwards formed right into a continuous profile via a die. The raw plastic material, frequently in the form of pellets, is fed into an extruder. Inside the extruder, the plastic undergoes heat and pressure, triggering it to thaw. The liquified plastic is after that required via a shaped opening, known as a die, to create a long, constant product. The extruded item is cooled down and after that reduced to the wanted length. The plastic extrusion procedure is thoroughly used in numerous sectors because of its adaptability, cost-effectiveness, and effectiveness.
Different Kinds Of Plastic Extrusion Techniques
Building upon the basic understanding of the plastic extrusion process, it is needed to discover the different strategies involved in this manufacturing technique. The two main strategies are profile extrusion and sheet extrusion. In profile extrusion, plastic is melted and developed right into a constant profile, commonly made use of to develop pipelines, rods, rails, and window structures. In comparison, sheet extrusion creates big, level sheets of plastic, which are normally further processed into items such as food packaging, shower drapes, and vehicle parts. Each strategy calls for specialized equipment and precise control over temperature level and pressure to make sure the plastic maintains its shape throughout cooling. Recognizing these methods is key to making use of plastic extrusion efficiently in contemporary manufacturing.

The Duty of Plastic Extrusion in the Automotive Market
A frustrating bulk of components in modern automobiles are products of the plastic extrusion process. This procedure right here has actually revolutionized the vehicle sector, transforming it into a more reliable, affordable, and flexible manufacturing industry. Plastic extrusion is mostly made use of in the manufacturing of different vehicle components such as bumpers, grills, door panels, and dashboard trim. The procedure supplies an uniform, regular output, enabling suppliers to create high-volume components with excellent precision and very little waste. The lightness of the extruded plastic parts contributes to the general reduction in automobile weight, enhancing gas effectiveness. The toughness and resistance of these parts to heat, cool, and effect enhance the long life of cars. Thus, plastic extrusion plays a crucial function in automobile production.
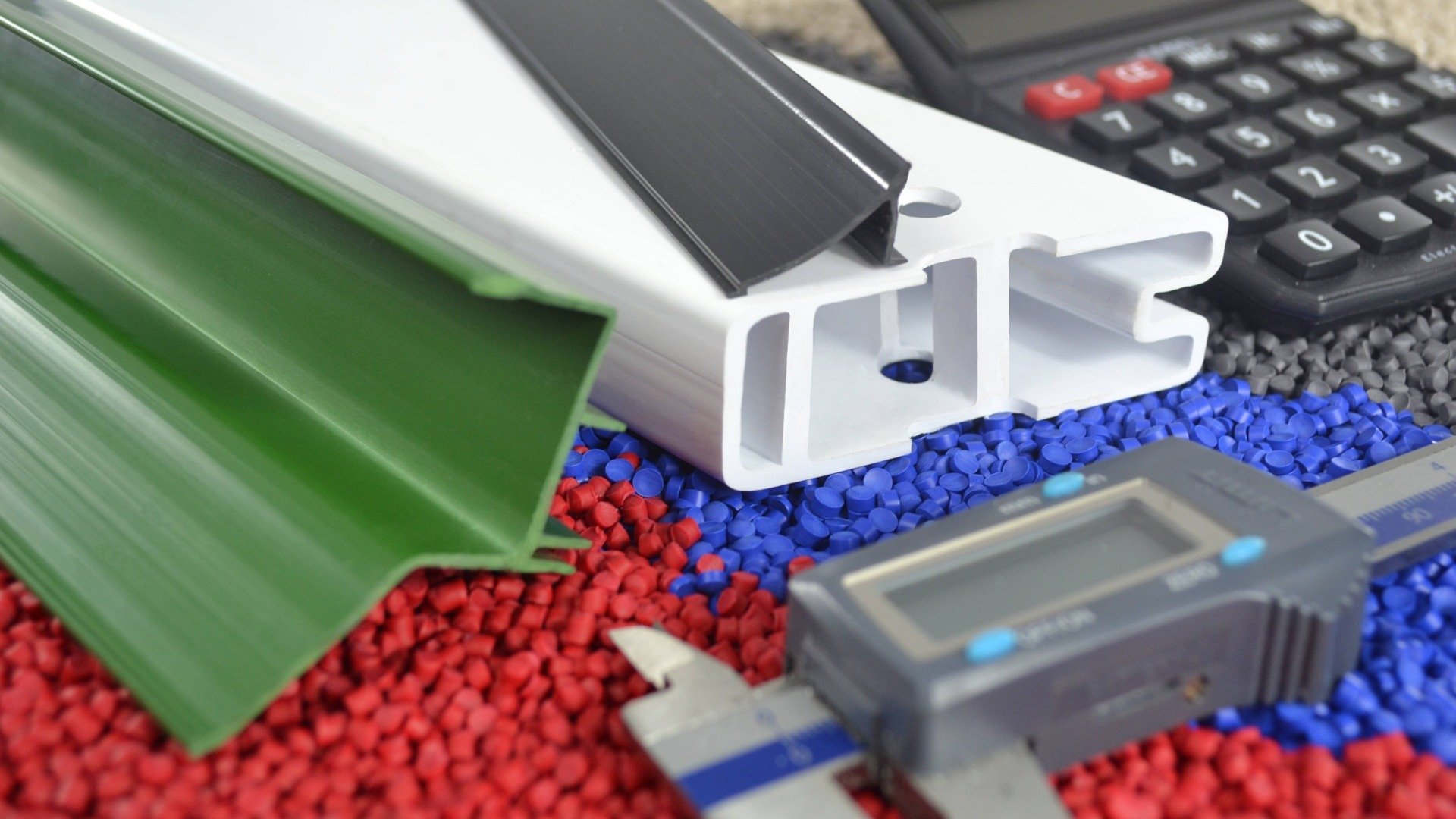
Applications of Plastic Extrusion in Durable Goods Manufacturing
Beyond its significant influence on the automotive sector, plastic extrusion confirms similarly efficient in the realm of consumer goods manufacturing. This process is vital in creating a broad selection of items, from food packaging to home appliances, playthings, and also clinical devices. The convenience of plastic extrusion allows makers to develop and create complicated shapes and sizes with high precision and effectiveness. Additionally, due to the recyclability of many plastics, extruded components can be reprocessed, minimizing waste and cost. The flexibility, adaptability, and cost-effectiveness of plastic extrusion make it a preferred choice for several consumer products producers, contributing considerably to the market's development and advancement. The environmental implications of this widespread usage require careful consideration, a topic to be reviewed further in the subsequent area.
Ecological Impact and Sustainability in Plastic Extrusion
The pervasive use plastic extrusion in producing welcomes scrutiny of its environmental ramifications. As important site a procedure that frequently makes use of non-biodegradable materials, the environmental effect can be significant. Energy intake, waste manufacturing, and carbon exhausts are all worries. Nevertheless, sector advancements are increasing sustainability. Efficient machinery decreases energy usage, while waste management systems reuse scrap plastic, decreasing resources demands. Furthermore, the development of biodegradable plastics offers a more environmentally pleasant choice. Regardless of these improvements, even more advancement is needed to reduce the environmental impact of plastic extrusion. As culture leans towards sustainability, producers must adjust to stay feasible, highlighting the significance of continual study and development in this area.
Verdict
In final thought, plastic extrusion plays an important function in modern-day production, specifically in the automobile and consumer products sectors. Recognizing the fundamentals of this procedure is essential to maximizing its benefits and applications.

The plastic extrusion process is thoroughly utilized in numerous sectors due to its flexibility, cost-effectiveness, and performance.
Building upon the fundamental understanding of the plastic extrusion process, it is essential to check out the numerous methods entailed in this manufacturing Read Full Report technique. plastic extrusion. In comparison, sheet extrusion produces large, level sheets of plastic, which are commonly additional processed into items such as food packaging, shower drapes, and automobile parts.An overwhelming bulk of parts in contemporary vehicles are products of the plastic extrusion process
Report this page